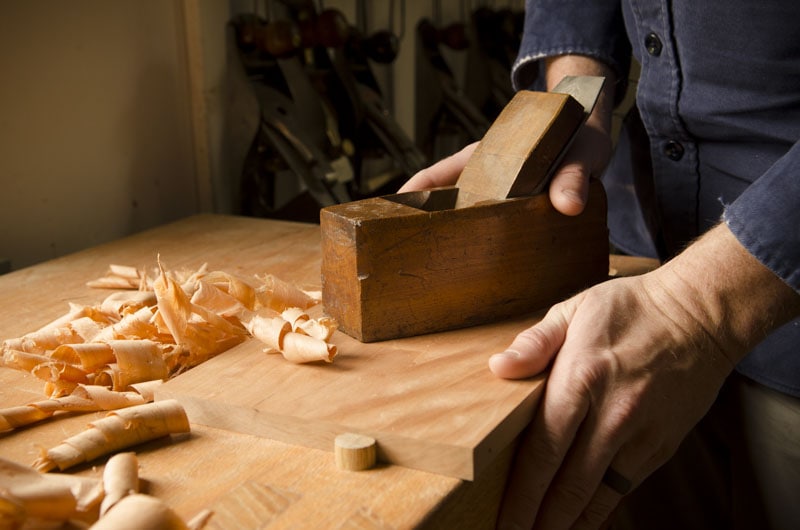
A disk sander has many benefits, including its speed finish and mitre gauge. These sanders tend to be a little less portable than some other models but can still produce the same high quality results. Look around to see which one best suits your needs. Below are some of the most important benefits of a Disk Sander. You can choose from a sander which combines both sanding techniques or a sander only that one.
For face sanding, you can use disk sanders
Disk sanders can be used as versatile sanding instruments. The rotating disk supports an aluminum or steel back plate that spins up and down to sand a material's face. The washer and center screw of the disc are hidden from view and do not extend into the work area. Benchtop disk sanders come with adjustable work tables for miter gauge slots or end cuts. Disc diameters usually range from four inches to eight inches. Larger models have capacities of 12 inches or greater.
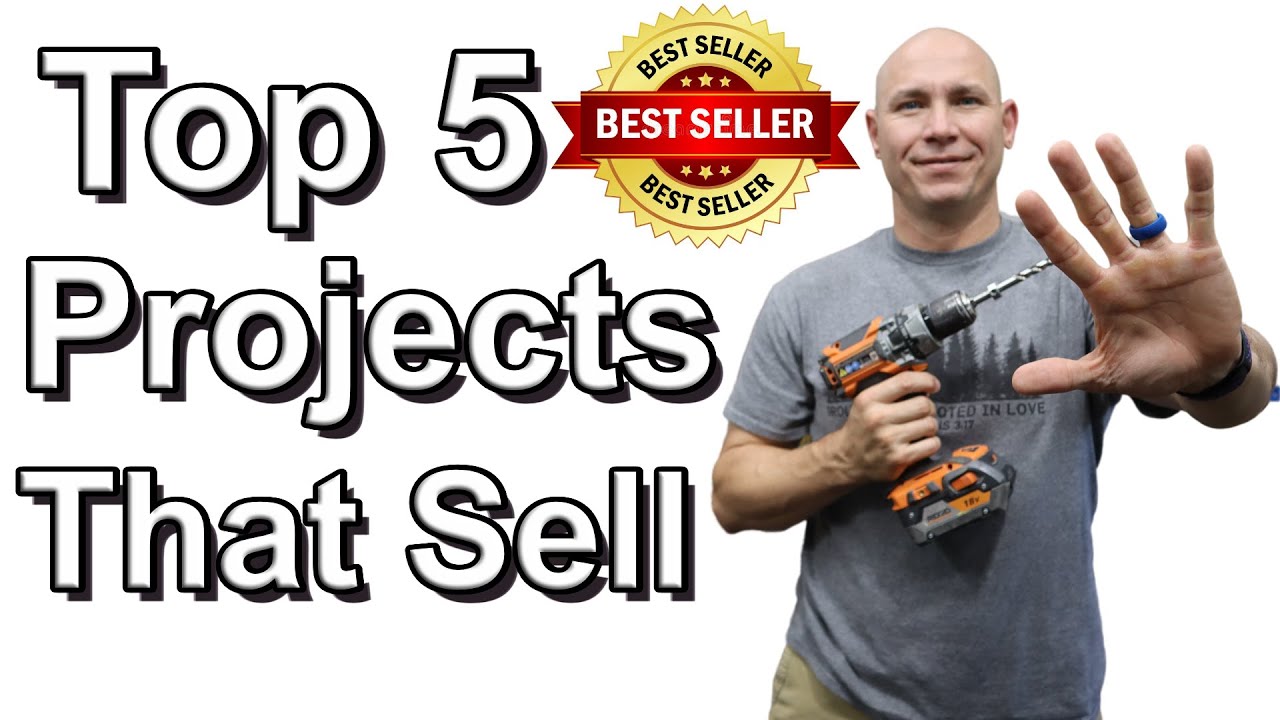
They are quick to finish
Disk sanders are a great option for speed. There are many sizes for disk sanders. These can be used on everything from small hobby machines to huge industrial plants. Most home shops use a 12 inch disk. The majority of disks are made from pressure-sensitive adhesive material. A disc sander is an excellent investment for projects that require a fast smooth finish.
They are lighter than other sanders.
A disc sander, a hand tool for smoothing small or thin cuts, is a hand tool. They are also smaller than other disc sanders. They are not as portable as other sanders, but are still useful for various hand jobs, such as sanding wood, plastic, and metal. They are small enough to be used on both small and large items and they are also very affordable. They can be used to smoothen and shape various materials.
They also have a mitre gage
A disk sander comes with many benefits, such as a mitre gauge. This allows the workpiece to be guided against the disc and prevents tearout. This feature also increases the fence height to protect your fingers against the edge of the blade. The miter gauge can be locked in with a clamp. This tip was provided by Bernard Lewan. Here's how to set it up.
They are equipped with a movable table
Setting the table's height or tilt is the first step to using a disk-sander. You should ensure that your workpiece is not too high when using a table with adjustable height. If it doesn’t, the workpiece might hit the sanding plate. Check all of the other controls on the table, including the power plant, carriage, table height, and quill lock. You can purchase a miter gauge extend if you need extra support.
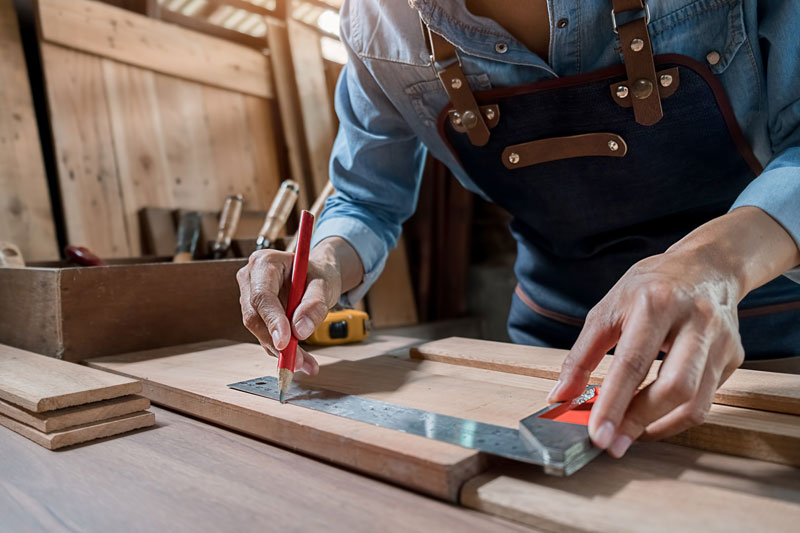
They have dust ports
The disk sander is associated with a dust collector housing. The dust collector housing surrounds all of the sander and the front half is exposed to the workpiece. To expose the whole disc, remove both the dust collector case and the front of the sander. For quick release of bolt 90, a hex wrench34 is provided. Bolt 90 must also be tightened to ensure that the bed 16 is in its vertical position.
FAQ
How much should a Woodworker Charge per Hour?
The hourly rate of a professional woodworker depends on many factors including experience, skill level, availability, location, etc.
An hourly wage for skilled woodworkers is between $20 and $50.
An hourly rate of $10 for a less skilled woodworker could be possible.
Can I make a living doing this?
Yes! In fact, most woodworkers already have it. According to U.S. Bureau of Labor Statistics (BLS), woodworkers earned a median annual salary of $34,000 in May 2012. This is much higher than the national median of $31,000 per annum.
Do you have any tips on starting a woodworking business?
It can be difficult to start a woodworking shop. You won't mind working hard if your hobby is something you love. You'll enjoy the challenge and rewards of owning your own business.
Remember that you may encounter unexpected problems when starting a new venture. You may run out of money suddenly. Maybe customers won't be willing to pay what you want. These situations are necessary for survival.
It is a good idea to create a separate bank account just for your company. You'll be able to track how much money comes in and out.
Where do you start when it comes to woodworking?
It is best to actually build furniture to learn how to make it. While you will need tools and make mistakes, you will eventually master the art of building furniture.
Begin by choosing the project that you want to finish. It could be something as simple as a box or as elaborate as a full-scale entertainment center. Once you have settled on a specific project, it is time to find a woodworker in your area who is experienced in such work. Ask them for their advice about the tools and where they can be found. You might even ask whether there's someone else you can talk to who does this kind of work.
What else should I know about woodworking in general?
It is easy to underestimate how much work it takes to make furniture. Finding the right type of wood is the most difficult aspect of this process. There are so many wood options that it can be difficult to choose the right one.
Another issue is that wood does not have the same properties. Some woods will crack or warp with time. Others will split or crack. Before purchasing wood, you should consider these factors.
How do you know which type of wood you are working with?
Always inspect the label when buying wood. The label should include information about the wood species and its moisture content as well as whether or not it has been treated using preservatives.
Statistics
- If your lumber isn't as dry as you would like when you purchase it (over 22% in Glen Huey's opinion…probably over 10-15% in my opinion), then it's a good idea to let it acclimate to your workshop for a couple of weeks. (woodandshop.com)
- Average lumber prices rose about 600 percent between April 2020 and May 2021. (familyhandyman.com)
- Woodworkers on the lower end of that spectrum, the bottom 10% to be exact, make roughly $24,000 a year, while the top 10% makes $108,000. (zippia.com)
- In 2014, there were just over 237,000 jobs for all woodworkers, with other wood product manufacturing employing 23 percent; wood kitchen cabinets and countertop manufacturing employing 21 percent. (theartcareerproject.com)
External Links
How To
How to join wooden boards without using nails
Woodworking is an enjoyable hobby. Woodworking can be a fun hobby because you can work with your hands to make useful objects from wood. There are times when two pieces of wood need to be joined together. This article will teach you how to do this to keep your woodwork projects looking great.
The first thing you'll need to do is cut off any rough edges from your pieces of wood before joining them together. Avoid leaving sharp edges that could lead to problems later. Now it's time to start glueing your boards together.
If you are working with hardwood, only one side should be glue. If you're using softwoods like pine or cedar, you should put glue on both sides. After applying the glue, press the boards firmly until they are completely stuck together. Before moving onto the next step, make sure the glue has dried completely.
After you have glued the boards together, drill holes in the joints where you intend to place screws. Depending on the type of screw that you use, the size of these holes will vary. For example, if your screw is a 1/2-inch wooden screw, drill a hole that is at minimum 3/4 inches deep.
After drilling the holes, you can drive the screws into your board's backside. Avoid hitting the board's top surface. Otherwise, you could ruin the finish. Be careful not to drive the screws too hard at the ends. This will avoid splitting in the wood's ends grain.
After your project is completed, you will need to protect it from the weather. You can either seal the entire piece of furniture or cover the top. Either way, you'll want to use a product that will last for years to come. Examples include oil-based varnishes and polyurethanes, shellac, lacquer and others.
These products can usually be found at any home improvement store. Just make sure that you buy the right kind for the job. Keep in mind that certain finishes can be toxic and should not be used indoors. Protective gear should always be worn when handling these finishes.