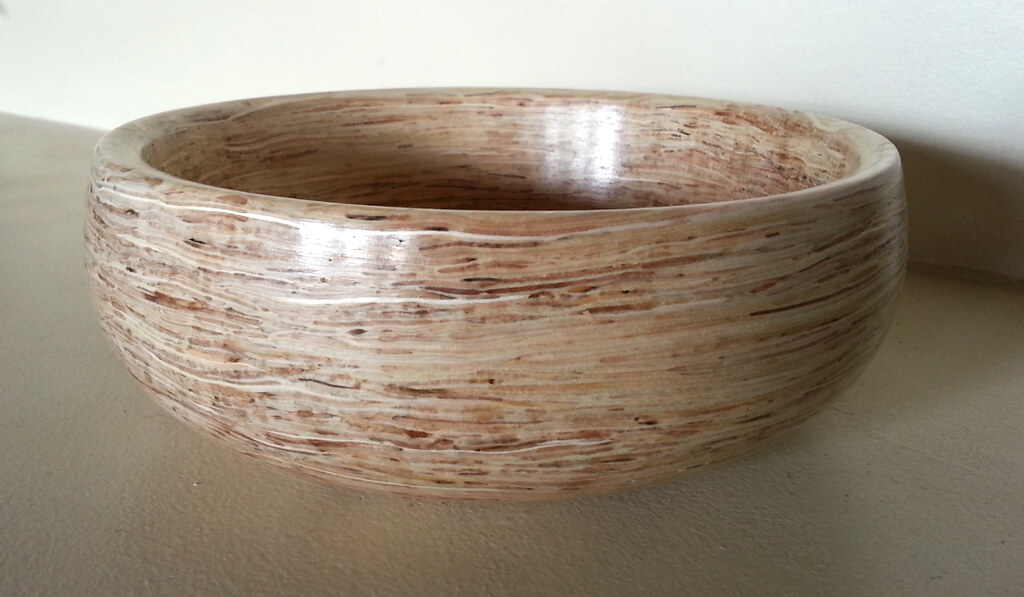
Philip Moulthrop began turning wooden in 1979. He learned his craft from his dad, Ed Moulthrop. He roughens out the green areas of trees from the southeast using a hand-forged chainsaw and lathe. He then finishes the bowl with several coats and refines it on his lathe. The entire process takes anywhere from four months to a year. Once they're done, you can either buy the bowls or give them as gifts.
Philip Moulthrop
Phillip Moulthrop bowl, a magnificent red leopard maple vessel is available. He developed the wood turning process, which has been a family heritage for three generations. Philip Moulthrop has made bowls for several notable museums and private collections. Here are some of their most renowned pieces. Read on for more information on this talented artist.
Philip Moulthrop, an American painter, was born in 1947. He began his studies in the arts at age 20 and discovered a love for woodworking. At the age of 16, he purchased his first machine and continued to improve his skills. His techniques were successful and he was able to produce beautiful vessels. This attracted the attention not only of the art community but also the President of the United States. After his work had been recognized, he started selling his products at local craft shows and galleries. This earned him international recognition.
Matt Moulthrop
The Matt Moulthrop-Bowls are a stunning example of Georgia’s rich wood turning tradition. The artist was born in Atlanta and received his BA and MBA from Georgia Tech. Although he spent a couple of years in the world of 9-to-5 jobs, he never forgot his passion for turning wood. He won national recognition for his bowls. His works can be seen at the ASU Art Museum and Carter Center, as well as the Racine Art Museum.
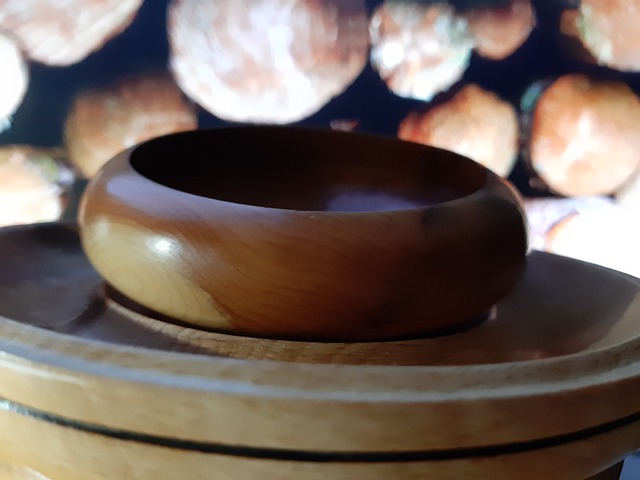
The Moulthrops are recognized for being world-class woodturners. They have works in many prominent collections in the United States as well as abroad. The Renwick Gallery of the National Museum of American Art holds some of Moulthrop's pieces, including his own. Collectors have collected many of his bowls. He gave each photographer an autographed copy of his family's memoir during a Smithsonian photo shoot.
Ed Moulthrop
Moulthrop began to turn bowls around 1970s. Soon after, he received a scholarship at Princeton University to study architectural design. Moulthrop spent a year in Vietnam and then resigned as an architect to pursue woodturning. His large-scale, turned bowls are internationally recognized and can be found in museums like the Museum of Arts and Design in New York and the White House Collection of American Crafts. These bowls can be made from domestic woods or polished to a crystal clear finish.
The rare Ed Moulthrop bowl measures nine inches across by fourteen inches and is made from wild cherry. These wood bowls may be purchased at Gump’s in San Francisco. Ed Moulthrop's wooden bowls are just one of many pieces on display. Visit the exhibition to get a better idea of his work. He also publishes a beautiful catalogue of his work. While it is possible to purchase the bowls from museums, it's best to visit his studio and see it in person.
The Eagle & Phenix Dam Series
This limited edition moulthrop series features wood from Eagle & Phenix Dam. A series of dams that once stood near Columbus, Georgia. The bowls retain traces from history and are made by Philip Moulthrop (local artists). They can be bid upon during museum hours and some of them will be sold live.
The Moulthrops have contributed to Georgia's growth of wood-turned bolles. The Moulthrop family has been making bowls for over 50 years. Three generations have contributed to the creation of this museum. Many of these pieces are highly prized for their large size and smooth, polished surfaces. His unique mosaic bowl technique of glue and thin branches attached to a turned bowl is also featured in the exhibit.
Matt Moulthrop's works
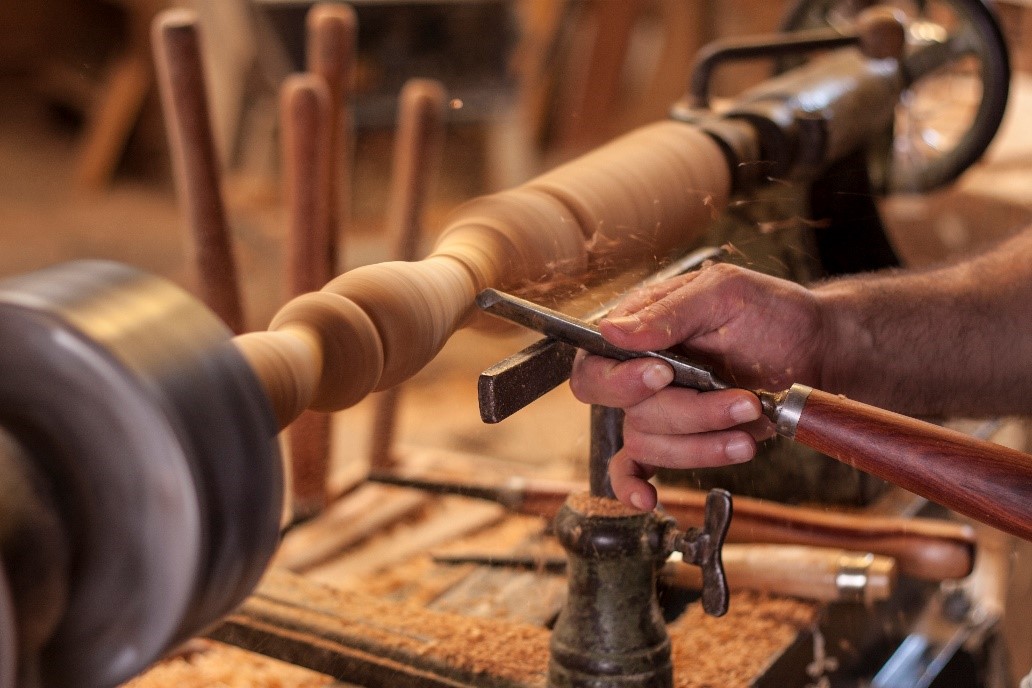
A son of Philip and Ed Moulthrop, Matt Moulthrop grew up around woodturning. He was taught by his father at an early age, and his passion for woodworking grew. Matt pursued a degree in business administration at Georgia Tech after earning his BA from the University of Georgia. He is the third generation of woodworkers. His work can be found in many prominent institutions, including the ASU Art Museum or the Carter Center. He is currently working on commemorative pieces for the Georgia Tech Alumni Association's 100th anniversary.
Georgia is not the only place he can turn wood. He travels to other parts of the world to find unusual wood. He transforms trees from around world using tools and an hand-forged lathe. This creates unique pieces. His pieces include wood harvested from trees that have fallen in the Southeast as also exotic locations such as volcanoes, underwater forests, and other places. His work is well worth a look if you like it!
FAQ
How can I tell what kind of wood I am working with?
When purchasing wood, always check the label. The label should detail the wood species, its moisture content and whether it has been treated or not.
How long does it usually take to complete a piece furniture?
It depends on which wood you choose, how complicated your design is and what amount of finishing you apply. Hardwoods, for example, require more maintenance than softwoods. Hardwoods can also be more costly than softwoods. They last longer and are more resistant to moisture. It takes between one and three months to finish a piece.
What is the difference in plywood and particleboard?
Plywood is made of layers of wood that are pressed together under pressure. Plywood can come in many thicknesses and is used for flooring and cabinets. Particle board is made from sawdust mixed with resin and then compressed into large blocks. This board is commonly used in home improvement projects. Both boards can be cut easily and are both durable.
What are the basics of woodworking?
The best way to learn how furniture construction is to make your own bench. You can use any wood you have in your home to complete this project. If you don't know what kind of wood to use, then go ahead and buy some cheap pine boards from Home Depot or Lowes. Once you have built your bench, you will need to sand it off and then finish it with a stain/varnish.
Statistics
- In 2014, there were just over 237,000 jobs for all woodworkers, with other wood product manufacturing employing 23 percent; wood kitchen cabinets and countertop manufacturing employing 21 percent. (theartcareerproject.com)
- Average lumber prices rose about 600 percent between April 2020 and May 2021. (familyhandyman.com)
- Woodworkers on the lower end of that spectrum, the bottom 10% to be exact, make roughly $24,000 a year, while the top 10% makes $108,000. (zippia.com)
- Overall employment of woodworkers is projected to grow 8 percent from 2020 to 2030, about as fast as the average for all occupations. (bls.gov)
External Links
How To
Here are some tips on how to drive nails in wood
When driving a nail into wood, it is important to first choose the correct size and kind of hammer. Claw hammers include mallets, claw hammers (sledgehammers), mallets, ball-peen hammers, hatchets, and mallets. Each type of hammer comes with its advantages and disadvantages. A claw hammer, for example, is the best choice if you need to hit nails hard. However, it's not easy to know exactly where the impact will land. A sledgehammer is useful for striking large areas at once but too heavy to be effective for smaller tasks.
After choosing the right hammer, place your hand flat against the side of the head so that the handle rests comfortably in your palm. Take the handle and hold it with both hands. But don't press down so hard you injure yourself. Hold the hammer straight up, keeping your wrist relaxed. Then swing the hammer back toward the ground, aiming for the center of the nail. You should feel the impact of the hammer striking the nail. You can practice swinging the hammer with a block or wood until you feel the rhythm.
The hammer should be held close to your body when you are ready to begin driving the nail. Position the nail, so it's perpendicular to the surface of the wood. Your eyes should be focused on the nail's tip. Move the hammer forward and then continue to move the hammerhead. You can repeat this several times, increasing your swing speed. Try adding power to your swings when you've mastered the technique. You can hold the hammer over your shoulder and forcefully bring it down. This way, you'll be able to put more energy behind your blows.
After you have nailed the hole, take the hammer off the nail. You can then remove the rest of the nails using a prybar or a screwdriver. Keep the nails heads in line with the surface of the board to prevent splitting the wood.