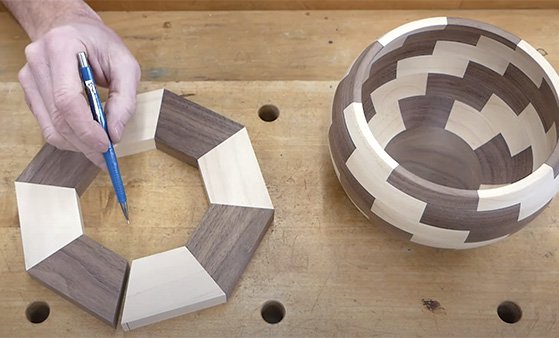
Philip Moulthrop started turning wood in 1979 after learning from his father Ed Moulthrop. Using a hand-forged lathe and chain saw, he roughs out the green sections of trees from southeastern regions. The bowl is then refined on the lathe and finished with several coats. The whole process can take between four months and a year. Once they're done, you can either buy the bowls or give them as gifts.
Philip Moulthrop
Phillip Moulthrop's bowl is made from red leopard maple. He developed the wood turning process, which has been a family heritage for three generations. Philip Moulthrop and his family have made many bowls that are now part of the permanent collections at several museums and private collections. Here are some their most iconic pieces. Continue reading for more information about this gifted artist.
Philip Moulthrop is an American artist who was born in 47. He studied general arts in his early 20s and developed an early passion for woodworking. At the age of 16, he purchased his first machine and continued to improve his skills. He developed his techniques, producing beautiful turned vessels that attracted the attention of the art community and even the United States President. After his work was acknowledged, he began to sell his pieces at local craft fairs. His work began to be recognized internationally.
Matt Moulthrop
The Matt Moulthrop Bowls are a beautiful example of Georgia's rich wood-turning tradition. The artist was a Georgia Tech graduate. He was a skilled woodturner, even though he worked a lot in the 9-to-5 world for a while. He won national recognition for his bowls. His works are displayed at the ASU Art Museum, the Carter Center and the Racine Art Museum.
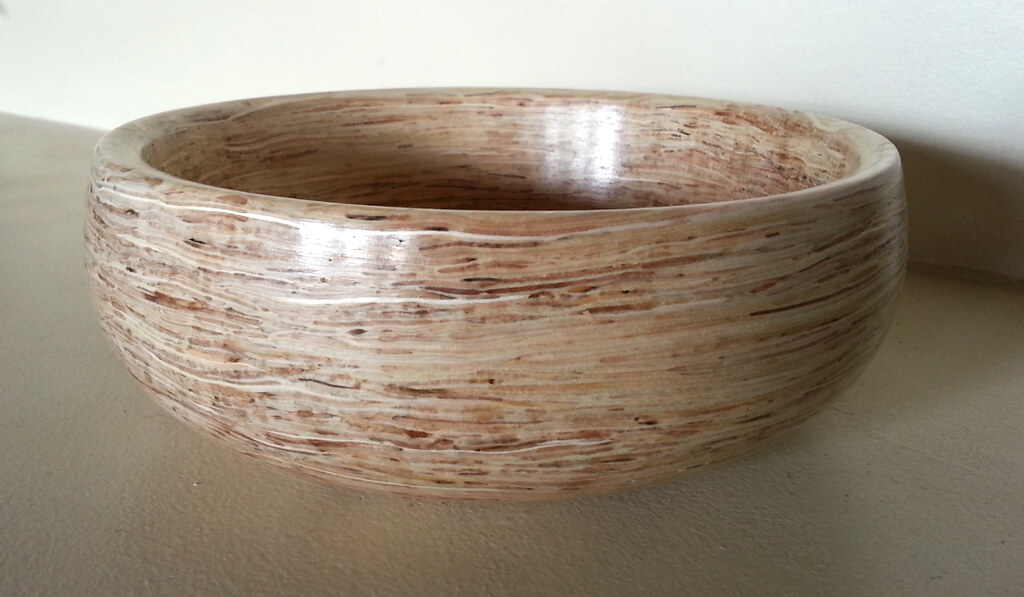
The Moulthrops were recognized as world-class woodturners. Their works have been placed in prominent collections across the United States and around the globe. Some of Moulthrop’s pieces are kept in the Renwick Gallery of the National Museum of American Art, which also includes his own. Collectors have collected many of his bowls. During a recent Smithsonian photo shoot, he gave each photographer a signed copy of his family's book.
Ed Moulthrop
Moulthrop started turning bowls in 1970s. Soon, he was awarded a scholarship to Princeton University to learn architecture. Moulthrop spent a year in Vietnam and then resigned as an architect to pursue woodturning. His large-scale turn bowls, which were internationally recognized, are now held in prestigious museums such as The White House Collection of American Crafts and Museum of Arts and Design. These bowls can be made from domestic woods or polished to a crystal clear finish.
The Ed Moulthrop wild cherry bowl measures nine inches wide by fourteen inches tall. These wood bowls may be purchased at Gump’s in San Francisco. Ed Moulthrop's wooden bowls are just one of many pieces on display. The best way to learn about the artist's work is to visit the exhibition. He also produces a beautiful catalog of his work. While it is possible to purchase the bowls from museums, it's best to visit his studio and see it in person.
The Eagle & Phenix Dam Series
This limited edition moulthrop series features wood from Eagle & Phenix Dam. A series of dams that once stood near Columbus, Georgia. The bowls have historical traces and were handcrafted in Atlanta by Philip and Matt Moulthrop. They are available to bid during regular museum hours. Additionally, a portion will be offered for sale live.
The Moulthrop Family has been instrumental in the development of Georgia's wood-turned wooden bowls. Three generations of Moulthrop families have been turning bowls over fifty years. The museum is proud of their works. Many of these pieces are prized due to their large size and smooth, polished surface. His unique mosaic bowl technique of glue and thin branches attached to a turned bowl is also featured in the exhibit.
Matt Moulthrop’s work
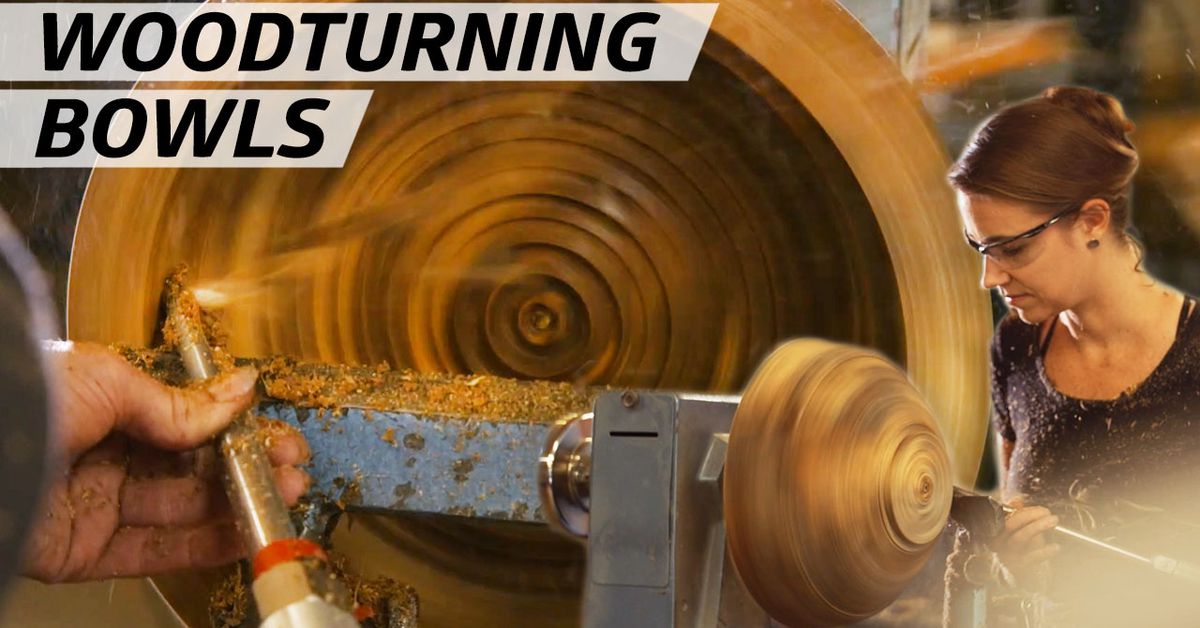
A son of Philip and Ed Moulthrop, Matt Moulthrop grew up around woodturning. His father was a pioneer in woodturning, and he continued to love it. Matt started his woodworking career after completing his BA degree at the University of Georgia. He also completed his MBA at Georgia Tech. He is now the third generation to make wooden vessels. His work can be found in many prominent institutions, including the ASU Art Museum or the Carter Center. He is currently working with commemorative pieces to mark the 100th anniversary for Georgia Tech Alumni Association.
Georgia is not home for the wood he transforms. To find unique wood, he travels all over the globe. He turns trees from around the world, using tools and a hand-forged lathe to create unique pieces. His pieces include wood that has been harvested from fallen trees in the Southeast, as well as exotic places like volcanoes and underwater forests. If you are a fan of his work, be sure to check it out!
FAQ
What would you recommend as a starting material for woodworking?
Start with softwood like pine, poplar and ash. These two are the easiest to master, then you can transition to hardwood.
What kinds of woods are good for making furniture?
Woods are classified according their hardness. Softwoods include pine, fir, cedar, and cypress. They are great for outdoor furniture as they resist rot. Hardwoods include oak, maple, mahogany, and teak. They can't withstand the elements outside so they're best kept indoors.
Do you know anything more about woodworking?
It is easy to underestimate how much work it takes to make furniture. Finding the right kind of wood is the most difficult part. It is difficult to choose between the various types of wood.
Another problem is that not all wood has uniform properties. Some woods will warp over time, others will split or crack. These are important considerations to make before you purchase wood.
Do you have any tips on starting a woodworking business?
It is hard work to start a woodworking company. If you are passionate about your hobby, it will not be difficult to put in the work. You might even enjoy running your own business.
It is important to remember that unexpected problems may arise when you start a new venture. You might run out money, or you may have to borrow unexpectedly. Perhaps customers won't pay you as much as you had hoped. You need to be ready for these situations if you want to survive.
It is a good idea to create a separate bank account just for your company. This will ensure that you always know how much money has come in.
Statistics
- Most woodworkers agree that lumber moisture needs to be under 10% for building furniture. (woodandshop.com)
- Average lumber prices rose about 600 percent between April 2020 and May 2021. (familyhandyman.com)
- The U.S. Bureau of Labor Statistics (BLS) estimates that the number of jobs for woodworkers will decline by 4% between 2019 and 2029. (indeed.com)
- Woodworkers on the lower end of that spectrum, the bottom 10% to be exact, make roughly $24,000 a year, while the top 10% makes $108,000. (zippia.com)
External Links
How To
How to join wood with no nails
Many people love woodworking. It's fun and relaxing because you can use your hands to make something useful from wood. You may need to join two pieces without the use of nails. This article will demonstrate how to do so to preserve the beauty of your woodwork.
First, remove any sharp edges from the wood pieces before you join them. Avoid leaving sharp edges that could lead to problems later. After you have completed this step, you are ready to glue your boards together.
When working with hardwood, glue should be applied only to one side. If you are using softwoods such pine or cedar, glue should only be applied to one side. Press the boards down until the glue is fully incorporated. Before you proceed to the next step, be sure to let the glue dry completely.
After you have glued the boards together, drill holes in the joints where you intend to place screws. Depending on what type screw you choose, the size of these holes will depend on how big they are. If you plan to use a 1/2 inch wood screw, drill a hole at least 3/4 inches in depth.
After drilling your holes, drive the screws into the board's backside. Be careful not to hit the front surface of the board, or else you'll ruin the finish. Be careful not to drive the screws too hard at the ends. This will prevent splitting in the end grain of the wood.
You'll need to protect your completed project from the elements. You can either cover the entire furniture or just the top. You'll want a product that lasts for many years. You can choose from oil-based varnishes or polyurethane, shellac and lacquer as examples.
These products can usually be found at any home improvement store. Just make sure that you buy the right kind for the job. Also, remember that some finishes are toxic and should never be used indoors. Always wear protective gear when handling any of these finishes.